Artificial Intelligence for Manufacturing Pilot Environment Themes
AI for manufacturing pilot environments are organized by seven interconnected technology themes:
1. Synthesis, Recycling, and Characterization: The heartbeat of the facility will consist of autonomous systems to synthesize feedstock materials, characterize the structure, chemistry, and performance of samples/witness coupons, and recycle used/spent materials, samples, and scraps into new feedstocks. This area will accept and transmit materials and samples from and to each of the other six themed areas. A first pilot project will develop data architecture that links inspection and characterization systems to manufacturing systems information in each other theme, enabling digital twins for products that are used to provide insight into advanced processes, production operations, and product quality at 5X greater speed and lower cost.
2. Solid State Batteries: AMPF will include facilities specific to next-generation solid state bat-teries and battery recycling technologies in support of GA and more broadly U.S. battery manufacturers and recyclers. A first pilot project will develop in-process monitoring sensors for roll-to-roll cathode manufacturing systems and machine learning models that provide real-time, continuous process optimization, accelerating cathode development cycles by years.
3. Metals Manufacturing: Transcending and impacting nearly every manufacturing sector, AMPF will innovate and de-risk metals robotic manufacturing, additive manufacturing, hybrid manufacturing, metamorphic manufacturing, traditional manufacturing, and recycling. A first pilot pro-ject will integrate open robotic systems into machine tools to produce a low-cost metal hybrid (additive + subtractive mfg.) system. The system will be programmed with CAD/CAM tools provided by industry partners and transitioned to technical colleges, industry, and university partners.
4. Concrete and Timber Construction: AI manufacturing innovations to increase constructabil-ity and environmental sustainability using concrete, which accounts for 8% of global and 5.31% of GA CO2 emissions and timber, will in total offset 8% of GA CO2 emissions by 2035. A first pilot project will utilize large-scale 3D printers to rapidly generate and prototype reusable low-cost concrete molds that include build paths for implanting sensors that provide data for digital twin models of structure health and performance for the construction industry.
5. Polymer Fiber Reinforced Composites: AMPF will provide innovation facilities to the Center for Composite and Hybrid Materials Interfacing, a collaborative Industry-Academia consortium that intends to dramatically improve composite and hybrid structures are joining and repair operations. A first project will develop AI capable of generating a quality report and in service repair plan using data from manufacturing process monitoring sensors.
6. Hypersonics: In support of GA hypersonics industry and national security needs, AMPF will enable transformative scale-up innovations for manufacturing, qualification, and recycling of un-classified geometries made using ultra-high temperature materials including refractory alloys, carbon-carbon composites, and ceramic matrix composites. A first pilot project will create machine vision inspection capabilities for these extremely high temperature manufacturing environments.
7. Augmented and Extended Reality Materials Handling: Humans are the most superior material handling system available to manufacturers for lower volume runs; automated handling systems retain and onshore U.S. manufacturing jobs for high volume markets. Augmented and ex-tended reality (AR/XR) can upskill the current workforce for new tasks, ensuring that their work is error free by providing guidance to the worker in operations such as assembly. Furthermore, when coupled with AI trained by experienced workers, it allows the next generation employees to learn from them, even after they retire. XR will also enable training using digital twins to simulate 1,000,000+ ft2 warehouses, global supply chains, and more within AMPF for purposes of innovating materials handling technologies and supply chains for the future. An initial pilot project will develop AR to increase performance of humans loading machine tools and parts to 100%.
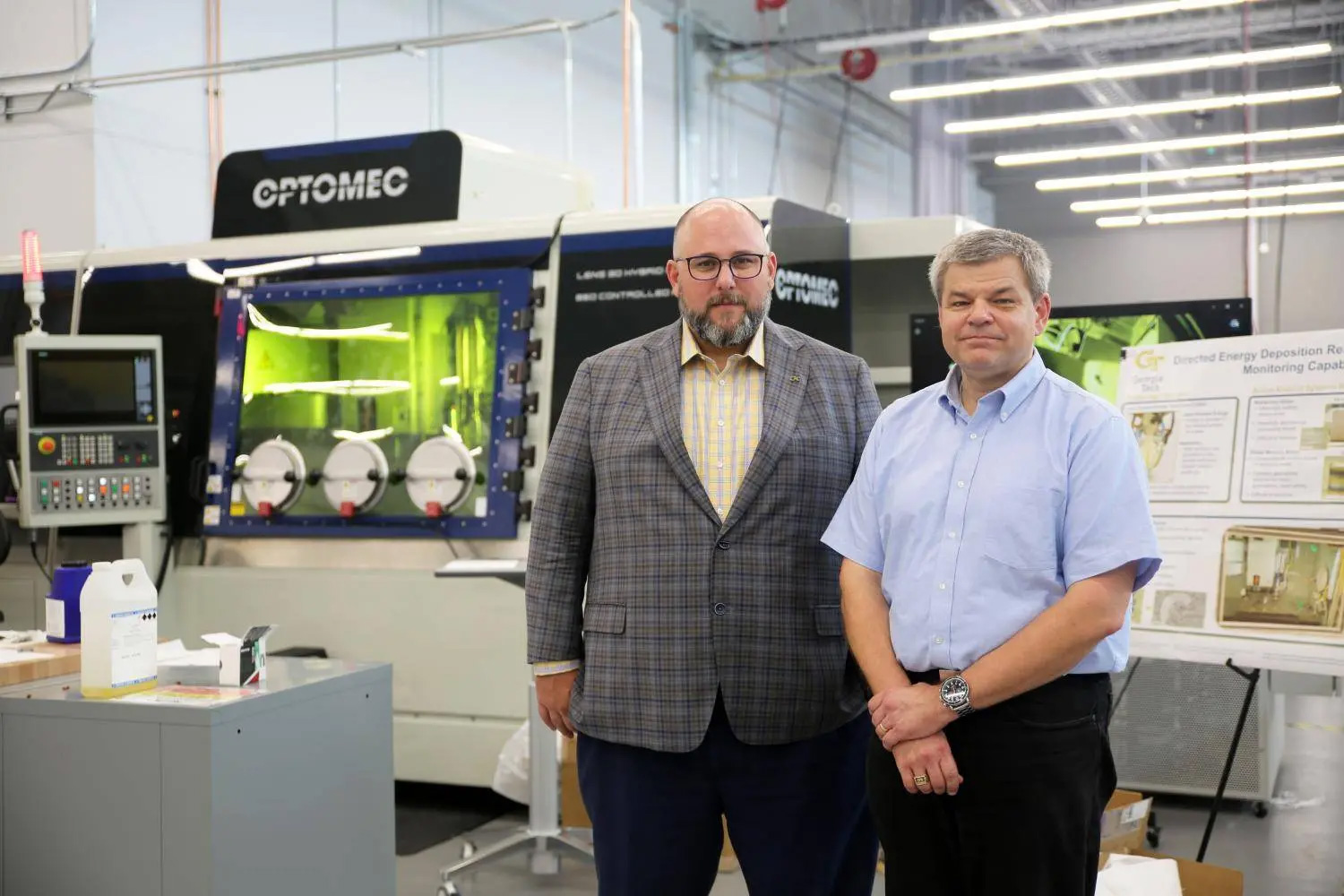
Aaron Stebner (left), associate professor in the George W. Woodruff School of Mechanical Engineering and the School of Materials Science and Engineering, and Tom Kurfess (right), executive director of the Georgia Tech Manufacturing Institute, lead the Advanced Manufacturing Pilot Facility (AMPF). Georgia Tech is helping to build AI and manufacturing in Georgia and the southeast. Learn more >>